The crawler crane sprocket, also known as drive sprocket, is a critical component of a crawler crane’s undercarriage system. It is vital in providing traction, stability, and power transmission for efficient and safe crane operations. Understanding the proper usage of crawler crane sprockets is essential to ensure optimal performance and longevity.
the position of sprocket for crawler crane
To ensure a better understanding of how to use a crawler crane sprocket, it is important to know its position.
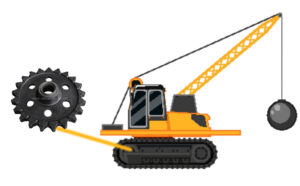
The sprocket for crawler crane is typically located at the rear of the crane’s undercarriage. It is positioned at the end of the track frame, where it engages with the track shoes. The sprocket consists of teeth or projections that mesh with the track shoes, providing traction and facilitating the movement of the crawler crane.
How to use a crawler crane sprocket?
Here is a step-by-step guide on the proper use of a crawler crane sprocket, five steps help you install and use sprocket correctly.
Step 1 Select the appropriate sprocket
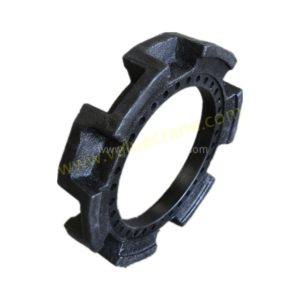
Hitachi KH180 sprocket
Choose a sprocket that is compatible with the make and model of your crawler crane. Consider factors such as load capacity, terrain conditions, and project requirements when selecting the sprocket.
Take the Hitachi KH180 sprocket as an example, based on its crawler crane model KH180 which is designed for heavy lifting and construction projects, the KH180 sprocket must enables it to traverse rough and uneven terrain and own high load capacity.
Step 2 Proper installation
Begin by preparing the necessary tools and equipment. Position the crane on stable ground and engage the brakes. Remove the old sprocket and inspect the track frame for any damage or misalignment. Clean the mounting surfaces and apply lubricant as recommended. Carefully position the new crawler crane sprocket, aligning it with the track chain. Securely fasten the sprocket to the track frame, following the manufacturer’s torque specifications. Reconnect the track chain and ensure proper tension. Conduct a final inspection before testing the crane’s operation.
Step 3 Track shoe alignment
Ensure proper alignment between the sprocket teeth and the track shoes. Regularly adjust the tension and alignment of the track system to maintain optimal engagement with the sprocket. Misalignment can cause premature wear and affect the crane’s performance.
The signs of sprocket misalignment
Misalignment of the crawler crane drive sprocket can lead to various issues that affect crane performance and safety. Signs of misalignment include uneven track wear, abnormal noises during operation, excessive vibrations, reduced performance in terms of traction and lifting capacity, track chain slack or tension issues, and premature wear on sprocket teeth.
Step 4 Terrain adaptation
Adjust the operation of the crawler crane based on the terrain conditions. Adapt the crane’s movement, speed, and operation to accommodate different terrains, such as soft soil, uneven surfaces, or steep inclines. This helps reduce stress on the sprocket and other undercarriage components.
Step 5 Regular cleaning
Keep the sprocket for crawler crane clean and free from debris. Regularly clean the sprocket to prevent excessive buildup, which can affect its performance and lead to premature wear.
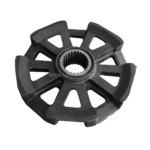
Common Mistakes to Avoid When Using a Crawler Crane Sprocket
When using a crawler crane sprocket, there are certain actions that should be avoided to ensure safe and proper operation.
abnormal noises
If you hear unusual noises like grinding or clicking during crane operation, do not ignore them. These noises could indicate drive sprocket misalignment or other problems that require immediate attention.
Overloading the crane
Avoid exceeding the crane’s lifting capacity or operating beyond its designated load limits. Overloading can put excessive strain on the sprocket and other components, leading to premature wear or failure.
Using the wrong size
Ensure that the selected sprocket is the correct size and type for the specific crane model. Using an incompatible or incorrect drive sprocket can lead to poor engagement with the track chain.